The engineering and facilities team at UI Pharmaceuticals, the College of Pharmacy’s FDA-registered drug development and manufacturing organization, has been working on innovative ideas and solutions to overcome process and mechanical challenges with the College’s unique pharmaceutical fill-line equipment.
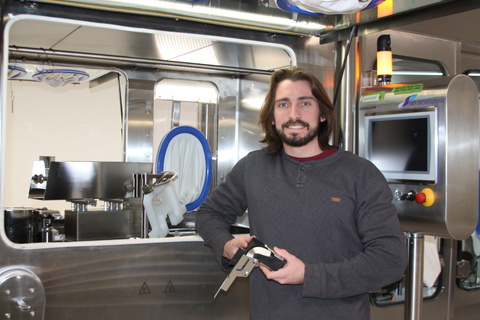
Because it’s a newly installed system, much testing needs to happen to work out any kinks and ensure everything runs smoothly. Since such testing began last fall one problem in particular has stuck out: vial caps in the automatic capper sticking in the cap transport system.
“It was a massive issue,” said UI Pharmaceuticals Assistant Process Engineer Garret Hinson, fondly referred to as ‘the capper keeper.’ “In fact, it got to the point where I was having to have my hand next to the system to shake the chute so caps would move through the system without becoming stuck.”
During the past couple of months, Hinson has been working to solve the problem. He looked at the whole transport system and diagnosed the transition assembly as the culprit. This portion of the cap transport system contains a very complex curvature to change the orientation of the caps.
“The piece had a much harder curve on top, along with other issues, that were detrimental to the design and flow of the caps,” said Hinson. “It caused friction, reduction of back pressure, and poor alignment, which led to caps sticking.”
Hinson had ideas on how to fix it and wrote a 20-page proposal to the supplier. Unfortunately, the company reported it would take five weeks to make the changes and ship a new piece – and UI Pharmaceuticals would have to do the design drawings.
Hinson said the long lead time was going to derail the project timeframe.
So, he turned to the University of Iowa Health Care Medical Instruments Shop to create an improved transition assembly piece. But because it was a piece with a lot of angles and curves, they couldn’t do it. So, they recommended Protostudios, the University of Iowa’s 3D printing lab.
The first printing was done using carbon fiber composite. In testing, Hinson learned this wasn’t compatible with required chemical sterility.
The next printing used plastic material and also had a couple of design iterations, including a bigger radius curve, to aid alignment. It’s currently being tested in the fill line, and so far, 4,000 caps have run without a single stick.
It took just one week from accepting the project to installing the latest version into the transport system.
“Teaming up with Protostudios has been of great benefit to UI Pharmaceuticals and keeping the project on track,” said Louay Ghonaym, director of engineering and facilities for UI Pharmaceuticals.
“Teaming up with Protostudios has been of great benefit to UI Pharmaceuticals and keeping the project on track,” said Louay Ghonaym, director of engineering and facilities for UI Pharmaceuticals. “The highly skilled Protostudios team and their state-of-the-art rapid prototyping equipment with the wide range of materials available have allowed us to develop the prototypes, modify them and finalize designs in a very short period of time.”
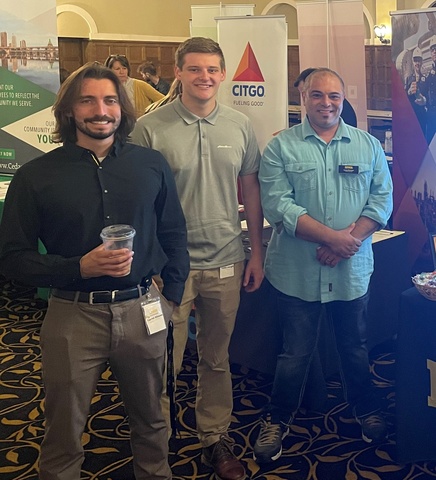
He added, “We are very pleased and excited to collaborate with Protostudios to achieve project completion and to maintain a long-term partnership not only for process improvement on current equipment but also on projects that are forecasted in the near future.”
Spencer Kuhl, operations director at Protostudios, shared Ghonaym’s sentiments.
“The UI Pharmaceuticals Engineering team has been great to work with,” he said. “Louay Ghonaym and his team had very specific design improvement requests on the bottling line components in addition to special material considerations. With our unique combination of design talent, materials expertise, and state-of-the art prototyping equipment, we were able to produce new iterations of parts that were designed, 3D printed for testing, and machined in the final materials. We look forward to working with the engineering team on future collaborations.”
The UI Pharmaceuticals’ new fill line is one-of-a-kind because it can run multiple different vial sizes, from 2 ml all the way up to 100 ml. The team’s perseverance in fixing the fill line capper problem and keeping testing on track is a testament to their commitment to the department’s mission: to improve quality of life and be the premier partner for academic, biotech, and government to advance patient access for new therapies and to support pharmaceuticals education initiatives.
“The engineering and facilities team demonstrated creativity and persistence in solving equipment design issues using printed components. Their approach enabled us to better pinpoint and solve equipment design issues, enabling the progression of start-up activities and improved functionality of the equipment,” said Dennis Erb, UI Pharmaceuticals managing director.